For our 225hp Merc OptiMax (outboard)
by Robin
First, let me preface this blog post with the fact that I am not a mechanic, although I did assist through most of this process with my hubby. He is the brilliant mind behind all our repair work. I do not claim to remember all the names of lubes, solvents, grease, epoxies, & specific pieces BUT, I think I do a really good job for a wife. I know way more about mechanical things than I ever thought I would when I got married. But enough of me.... onto the real star of the blog.
Here are the upper & lower cases of the powerhead. Everything has been disassembled, any glues or gasket fragments were removed and Jack sprayed some special degreaser to clean any gunk or debris out of the engine. This is a very important step that should not be skipped. After sitting, Jack hosed it down to wash off the debris.
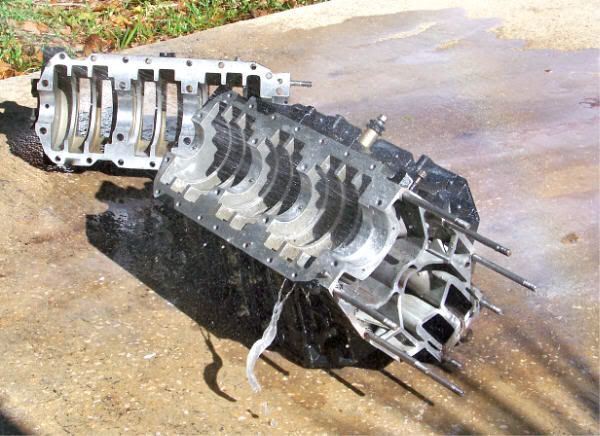
It's is sparkling clean. Those 6 main grooves are where the pistons & their arms will fit through to attach to the crankshaft (removed at this point).
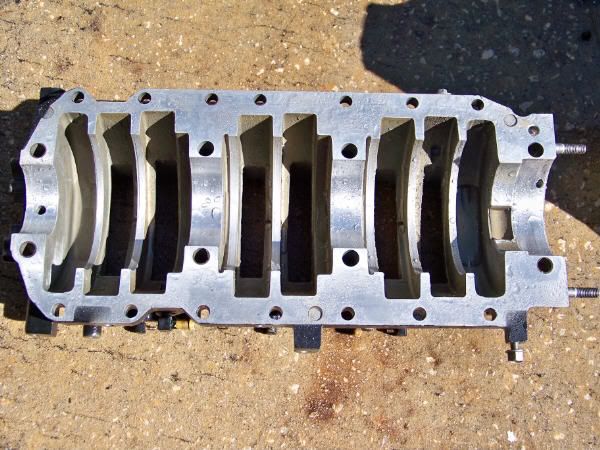
If you look very carefully at the black side of the powerhead, you will see little "spickets" where it looks like something is attached to the metal part. Those are for the oil lines. Jack took the time to make sure each one of those lines was free & clear of debris. We did this with a high-pressure air compressor attachment.
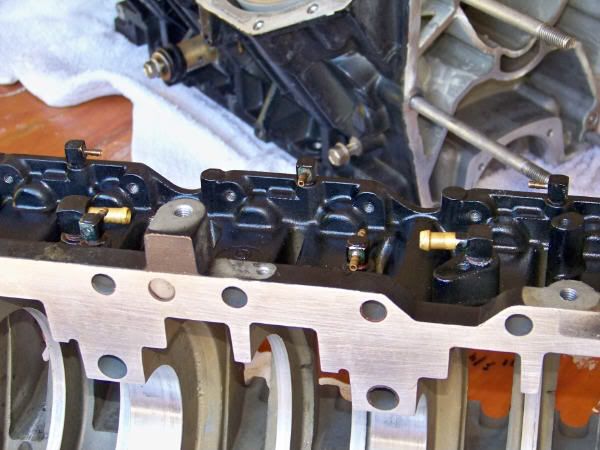
Then, Jack put it lots of grease into all the little areas between the pairs of pistons.
There are holes that he is filling.
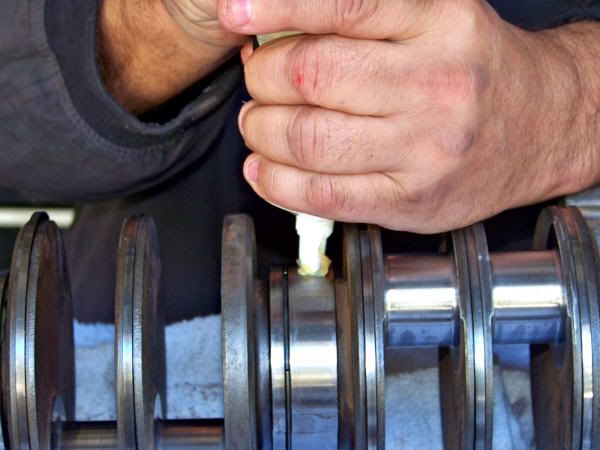
This is the lubricant that he used.
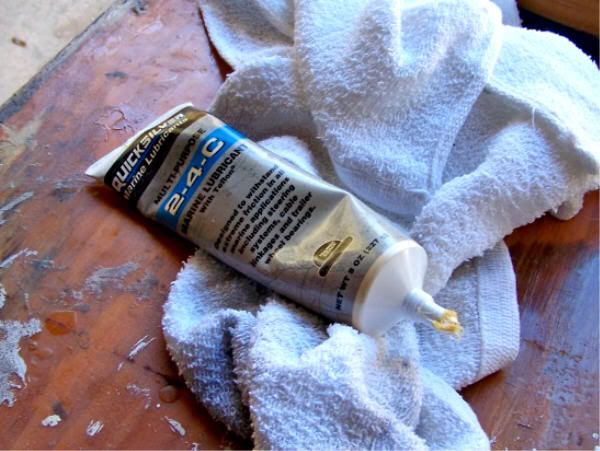
Next, we prepared the table with tools to begin the insertion of the pistons. If I remember right, Jack also took this time to replace a couple of the o-rings that go in on the upper end of the crankshaft, which were boogers to get out. BUT, we did it. So, at this point, we have pistons which need new rings assembled onto the end of them. I probably should have taken a picture of that. There are 2 of them. It was my job to remove the old so that explains why there are no pictures of it.
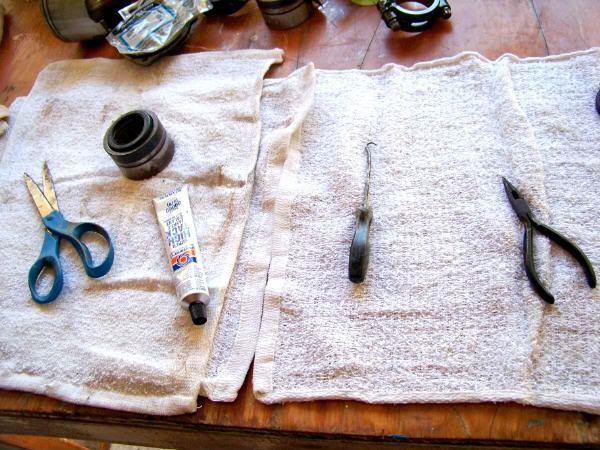
While I did that, Jack took the new rings that he ordered and according to specs, tried to fit them the best with each of the cylinder sleeves. It's an imperfect world out there, so you want to stay in a special range of a gap at the ends of the rings. (Rings have a break-point. I'm not explaining myself very well.)
If you look below where the arrow is, the ring is being checked in this sleeve and if the gap is too much, he has to find a bigger ring. Comprende'?
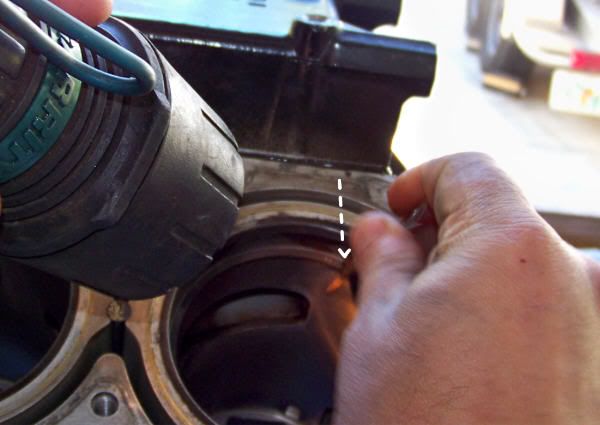
After the rings were matched to pistons, we put them on. Then Jack used this ring compression tool to hold them down (because they're a bit springy), then the piston is carefully slid up into position. Then, you remove the blue ring compressor and the rings spring to make a tight fit into the cylinder. The better the fit, the better the pressure, hence better the rpms & horsepower being made by the engine. Are you still with me??
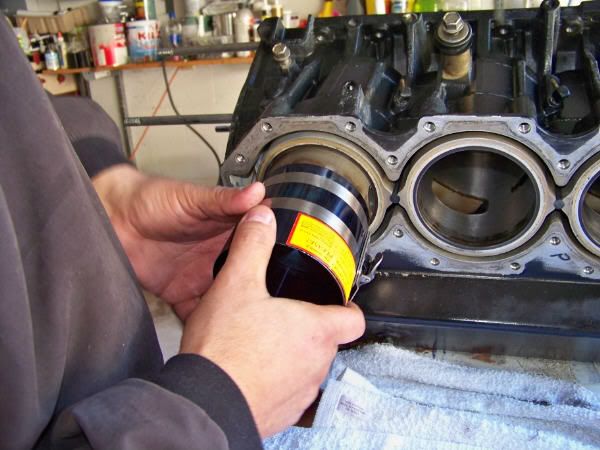
Jack is greasing the needle bearings and putting them into their "thing". There are two of these things and they fit on the inside of the arm of the piston that rotates round and round the crankshaft. I was dreading this part of the job most of all, but it turns out, it wasn't so bad. I did the other 5 of them. The grease keeps everything moving easily initially until the engine gets the oil flowing freely. BUT, the "ace in the hole" for the grease is that it keeps those stinkin' bearings from falling out. Think pliable glue. LOVE IT. This way, we didn't have to worry about them falling down into the deep recesses of the engine before Jack could tighten everything down. Whew!
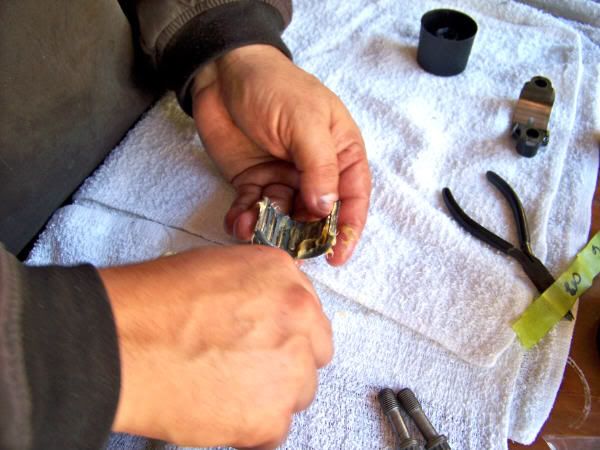
Here is the lower case with the crankshaft inserted & the pistons all attached to it. Yipee. We were almost done for the night at this point. Now, we had to attach the uppercase to the lower case.
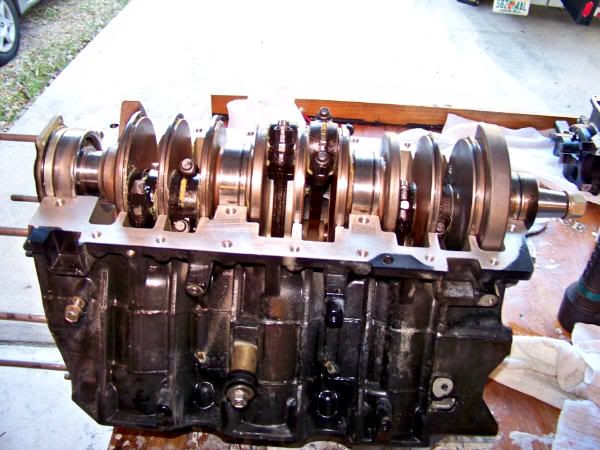
Forgive me for lack of info, but the red "goo" is a special epoxy that makes a gasket-type seal between the top & bottom of the cases. It's put on liberally and sealed down with long bolts & nuts.
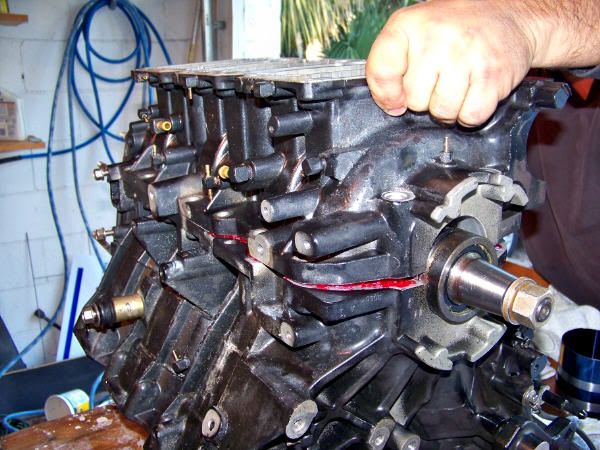
After this, we high-5'd each other, covered it up for the night and fell into a deep coma. Next morning, Jack added the parts that you see on top of the powerhead in the pic below. Then, he threw it on the hoist and I walked outside from doing breakfast dishes. I only had to assist in lining up a couple holes with bolts and throw on nuts. Here Jack is tightening everything down.
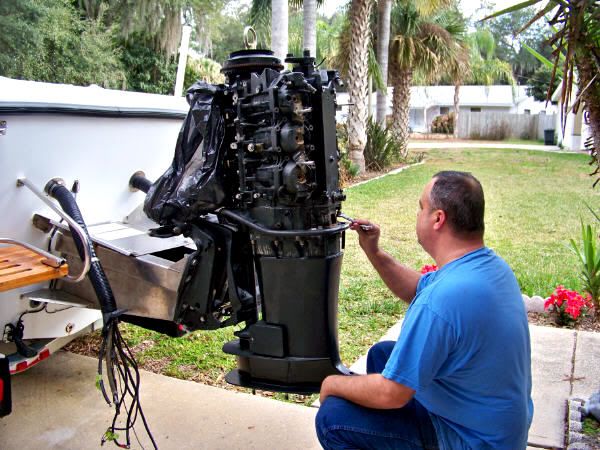
I'm thinking I wasn't too useful this day because I don't have a lot of pictures. Jack continued to add parts and oil lines. It's hard to see in the pic below but he used color-coded tie-wraps for securing lines. He would have to tell you the code because he gave it to me, I threw it in the vault and forgot it. Oops.
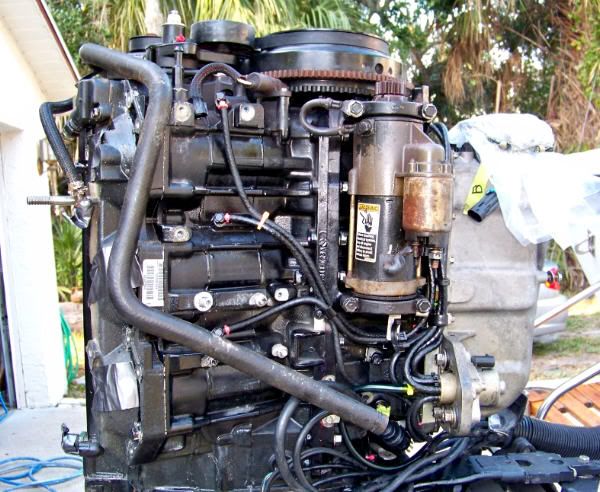
The next day, I believe he finished up with the lower foot (I did help a little bit of that.), matching up the intake pipe to it's 'home' and he put the electrical harness back into place.
More later....
Happy Fishing if the winds ever die down.
No comments:
Post a Comment